Continuous Improvement Methodologies: Enhancing Efficiency and Quality
Continuous improvement methodologies have become essential in today's rapidly evolving business landscape. Organizations across various industries are constantly striving to optimize their processes, enhance product quality, and meet customer demands more efficiently. In this blog post, we will explore the key concepts and methodologies behind continuous improvement, shedding light on how they can transform businesses for the better.
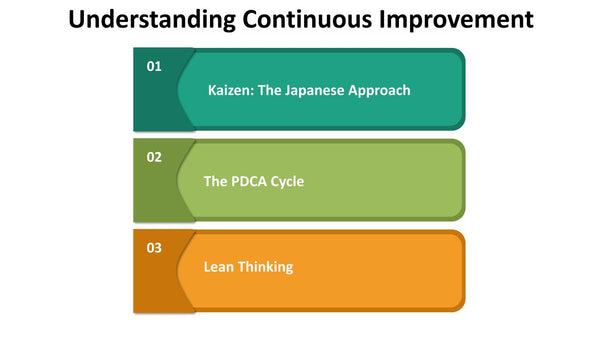
Understanding Continuous Improvement
Continuous improvement, often referred to as CI, is a systematic and ongoing approach to improving processes, products, or services. The primary goal of CI is to identify and eliminate inefficiencies, reduce waste, and enhance overall performance. Here are some fundamental aspects of continuous improvement:
-
Kaizen: The Japanese Approach
Kaizen, a term that means "change for better" or "continuous improvement" in Japanese, is at the heart of many CI methodologies. It emphasizes incremental, small-scale improvements made by employees at all levels of an organization. Kaizen encourages a culture of continuous learning and adaptation.
-
The PDCA Cycle
The Plan-Do-Check-Act (PDCA) cycle, also known as the Deming Cycle, is a widely used framework for continuous improvement. It consists of four steps:
- Plan: Identify areas for improvement and create a plan to address them.
- Do: Implement the plan on a small scale to test its effectiveness.
- Check: Evaluate the results and compare them to the desired outcomes.
- Act: If the results are favorable, standardize the improved process; if not, refine the plan and repeat the cycle.
-
Lean Thinking
Lean thinking is a CI methodology that focuses on minimizing waste and maximizing value for customers. It originated from the Toyota Production System and aims to reduce seven types of waste: overproduction, inventory, waiting, transportation, motion, defects, and over-processing.
Key Continuous Improvement Methodologies
-
Six Sigma
Six Sigma is a data-driven methodology that seeks to improve the quality of processes and products by reducing defects and variations. It relies on statistical analysis and defines defects as anything that deviates from customer specifications. Six Sigma projects follow a structured DMAIC (Define, Measure, Analyze, Improve, Control) approach.
-
Total Quality Management (TQM)
Total Quality Management is a holistic approach to CI that emphasizes the involvement of all employees in improving quality and customer satisfaction. TQM principles include customer focus, continuous improvement, employee involvement, and process management.
-
Lean Six Sigma
Combining the principles of Lean and Six Sigma, this methodology aims to eliminate waste while reducing defects and variations. Lean Six Sigma projects use the DMAIC framework but incorporate lean tools to streamline processes.
-
Agile and Scrum
Originally developed for software development, Agile and Scrum methodologies have found applications beyond IT. They promote iterative development, collaboration, and flexibility in project management. Agile principles align with CI by encouraging adaptability and responsiveness to change.
-
Theory of Constraints (TOC)
TOC is a CI methodology that identifies the single most limiting factor (the constraint) in a process and focuses improvement efforts on that constraint. By removing or mitigating the constraint, overall process performance can be significantly enhanced.
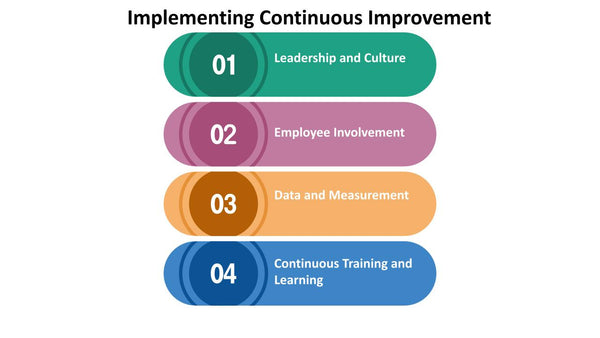
Implementing Continuous Improvement
-
Leadership and Culture
Creating a culture of continuous improvement starts with leadership commitment. Leaders should champion CI efforts, provide resources, and encourage employees to participate. A culture that values learning, experimentation, and innovation is essential for CI success.
-
Employee Involvement
Engaging employees at all levels is crucial for successful CI initiatives. Employees often have valuable insights into process inefficiencies and can contribute innovative ideas. Empowering them to take ownership of improvements fosters a sense of ownership and accountability.
-
Data and Measurement
Data is the backbone of CI. Organizations should collect and analyze data to identify areas for improvement and track progress. Key performance indicators (KPIs) help measure the impact of CI efforts and ensure alignment with strategic goals.
-
Continuous Training and Learning
CI methodologies evolve, and employees need to stay updated with the latest tools and techniques. Providing regular training and learning opportunities ensures that the workforce remains equipped to drive improvement initiatives effectively.
Case Studies of Continuous Improvement Success
To illustrate the real-world impact of CI methodologies, let's look at a few case studies:
-
Toyota Production System
Toyota's adoption of lean principles and continuous improvement led to remarkable efficiency gains in its manufacturing processes. The company's commitment to CI has made it a global leader in the automotive industry.
-
General Electric (GE)
GE implemented Six Sigma across its operations, resulting in substantial cost savings and improved product quality. This approach was instrumental in turning around the company's performance in the late 1990s.
-
Amazon
Amazon's relentless focus on customer satisfaction and continuous innovation is driven by a culture of continuous improvement. The company's ability to adapt and refine its processes quickly has contributed to its dominance in e-commerce.
Challenges and Pitfalls
While continuous improvement methodologies offer numerous benefits, they are not without challenges:
-
Resistance to Change
Employees and management may resist CI initiatives due to fear of change or lack of understanding. Overcoming this resistance requires effective communication and change management strategies.
-
Lack of Data and Measurement
Without accurate data and meaningful KPIs, it is challenging to identify areas for improvement or measure the impact of CI efforts. Organizations must invest in data collection and analysis capabilities.
-
Insufficient Leadership Support
CI initiatives can falter without strong leadership support. Leaders must actively champion and participate in improvement efforts to demonstrate their commitment.
Future Trends in Continuous Improvement
As technology and business practices continue to evolve, CI methodologies will also adapt. Some future trends in CI include:
-
Digital Transformation
The integration of technologies such as artificial intelligence, IoT, and data analytics will enhance CI efforts by providing real-time insights and predictive capabilities.
-
Remote and Hybrid Work
The shift to remote and hybrid work models will require organizations to adapt CI methodologies to new work environments and collaboration tools.
-
Sustainability
Sustainability will become a central focus of CI, with organizations seeking to reduce their environmental footprint and operate more responsibly.
Conclusion
Continuous improvement methodologies are not just tools for optimizing processes; they are pathways to organizational excellence. Embracing a culture of continuous improvement, supported by effective leadership, engaged employees, and data-driven decision-making, can lead to enhanced efficiency, higher product quality, and increased customer satisfaction. By staying adaptable and open to change, organizations can navigate the evolving business landscape and secure a brighter future.