Understanding Current Good Manufacturing Practices (cGMP)
Current Good Manufacturing Practices, commonly referred to as cGMP, are a set of regulations and guidelines that ensure the quality, safety, and efficacy of pharmaceuticals, food, and other products. These practices are crucial in maintaining product quality and safety throughout the manufacturing process. In this comprehensive blog post, we will delve into the world of cGMP, exploring its history, key principles, regulatory bodies, and its significance in various industries.
History of cGMP
The concept of cGMP was born out of necessity. In the early 20th century, numerous public health crises were caused by contaminated and adulterated products, including medicines and food. These crises led to the establishment of regulatory bodies such as the Food and Drug Administration (FDA) in the United States.
The cGMP regulations were formally introduced in the 1960s as a response to these issues. These regulations aimed to standardize manufacturing processes across industries to ensure the quality and safety of products. Over the decades, cGMP has evolved and expanded to cover various industries beyond pharmaceuticals, including food, cosmetics, and medical devices.
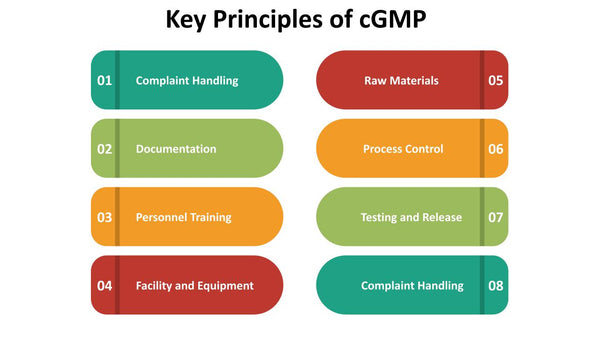
Key Principles of cGMP
cGMP is built on several key principles, which serve as the foundation for maintaining product quality and safety. These principles include:
- Quality Management: Manufacturers must have a comprehensive quality management system in place to oversee all aspects of production. This includes quality assurance and quality control measures to monitor and maintain product quality.
- Documentation: Accurate and thorough record-keeping is essential to track every step of the manufacturing process. Documentation ensures that processes are followed correctly, making it possible to trace issues and take corrective actions if necessary.
- Personnel Training: Properly trained personnel are crucial to ensure that manufacturing processes are conducted correctly. Training programs should cover cGMP requirements, safety protocols, and job-specific procedures.
- Facility and Equipment: Manufacturing facilities and equipment must be designed, constructed, and maintained to prevent contamination and ensure product integrity. Regular maintenance and calibration are essential to uphold these standards.
- Raw Materials: Manufacturers must use high-quality raw materials and establish controls to verify their identity and quality. This includes testing and supplier qualification processes.
- Process Control: Robust processes must be developed and maintained to ensure consistency and quality in the final product. This includes setting specifications, monitoring critical process parameters, and conducting regular process validation.
- Testing and Release: Rigorous testing of products is required before release to ensure they meet specified quality standards. This involves both in-process testing and testing of finished products.
- Complaint Handling: Procedures for handling customer complaints and product recalls must be in place to address potential issues promptly. This ensures that any quality or safety concerns are addressed swiftly to protect consumers.
Regulatory Bodies and cGMP
Different countries have their own regulatory agencies responsible for enforcing cGMP regulations. In the United States, the FDA plays a significant role in regulating cGMP compliance. In Europe, the European Medicines Agency (EMA) and the European Food Safety Authority (EFSA) oversee cGMP in pharmaceuticals and food, respectively. These agencies conduct inspections and audits to ensure manufacturers adhere to cGMP standards.
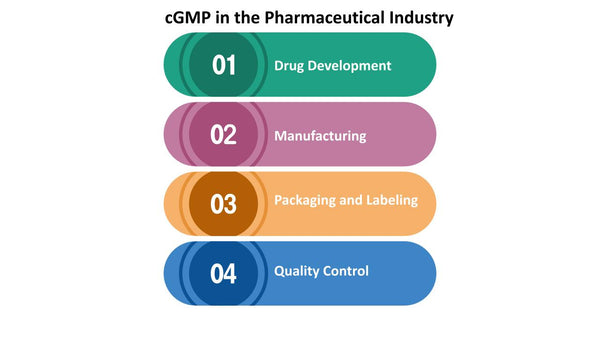
cGMP in the Pharmaceutical Industry
The pharmaceutical industry is perhaps the most well-known sector where cGMP compliance is crucial. Stringent cGMP regulations in this industry are in place to safeguard public health by ensuring that medicines are safe, effective, and of high quality. Key aspects of cGMP in pharmaceuticals include:
- Drug Development: From research and development to clinical trials, cGMP principles guide the entire drug development process. This includes documenting research findings, conducting clinical trials ethically, and ensuring the consistency of drug formulations.
- Manufacturing: Strict controls are maintained during drug manufacturing to prevent contamination and ensure consistency. Cleanroom environments, equipment validation, and adherence to batch records are essential components of cGMP compliance in manufacturing.
- Packaging and Labeling: Proper packaging and labeling are essential to ensure product identity and patient safety. Labels must accurately reflect product contents and usage instructions.
- Quality Control: Rigorous quality control testing is conducted at various stages of production to verify the product's quality. This includes chemical and microbiological testing to detect impurities or deviations from specifications.
cGMP in the Food Industry
In the food industry, cGMP is crucial for ensuring the safety and quality of food products. Key aspects of cGMP in the food industry include:
- Food Safety: Preventing contamination and ensuring safe handling and storage of food products are paramount. Food manufacturers must implement sanitation programs, pest control measures, and allergen management to protect consumers.
- Quality Assurance: Quality control measures, including sensory evaluation and laboratory testing, are used to maintain consistent product quality. This includes monitoring for factors such as taste, texture, color, and nutritional content.
- Labeling: Proper labeling ensures consumers have accurate information about food products' contents and nutritional value. Food labels must meet regulatory requirements, including ingredient lists, nutrition facts, and allergen declarations.
- Traceability: Manufacturers must have systems in place to trace the source of ingredients in case of recalls or contamination issues. This allows for swift and precise action in addressing any safety concerns.
cGMP in Other Industries
While pharmaceuticals and food are primary industries subject to cGMP regulations, these principles are also relevant in other sectors, including cosmetics, dietary supplements, medical devices, and even the cannabis industry. The specifics of cGMP compliance may vary, but the core principles remain the same – ensuring product quality and safety.
In the cosmetics industry, for example, cGMP guidelines focus on ingredient safety, product testing, and quality control. In the medical device industry, cGMP regulations ensure the safety and effectiveness of devices such as surgical instruments and diagnostic equipment.
In the emerging cannabis industry, cGMP compliance is becoming increasingly important as regulatory standards evolve to ensure the safety and quality of cannabis-based products.
Challenges and Compliance
Achieving and maintaining cGMP compliance is not without challenges. Manufacturers often face issues such as changing regulatory requirements, global supply chain complexities, and the need for ongoing training and education of personnel. However, the benefits of cGMP compliance, including enhanced product quality, consumer trust, and regulatory approval, outweigh the challenges.
Compliance with cGMP regulations requires a holistic approach, including:
- Investment in Infrastructure: Ensuring that manufacturing facilities and equipment meet cGMP standards. This may involve upgrading facilities, implementing quality control measures, and adopting modern technologies.
- Training and Education: Continuously educating personnel on cGMP requirements and best practices. Training programs should be robust, covering regulatory updates, quality control methods, and safety protocols.
- Regular Audits and Inspections: Proactively identifying and addressing compliance issues through internal audits and inspections. Regular self-assessments and external audits by regulatory agencies help manufacturers stay compliant.
- Risk Management: Implementing risk-based approaches to identify and mitigate potential hazards in the manufacturing process. This includes conducting risk assessments, developing contingency plans, and ensuring the safety of products in the event of unexpected incidents.
Conclusion
Current Good Manufacturing Practices (cGMP) are a vital set of regulations and guidelines that play a critical role in ensuring the quality, safety, and efficacy of products in various industries. From pharmaceuticals and food to cosmetics and medical devices, cGMP compliance is essential to protect public health and consumer confidence. As regulatory standards continue to evolve, it's imperative for manufacturers to stay current with cGMP requirements and uphold the highest standards of product quality and safety.