The Power of Corrective and Preventive Action (CAPA)
In the dynamic landscape of modern industries, ensuring the highest quality standards is paramount. One of the key methodologies that organizations employ to achieve and maintain quality excellence is Corrective and Preventive Action, or CAPA. In this comprehensive blog ,we will take a deep dive into CAPA, unraveling its significance, the intricacies of its implementation, best practices, challenges, and real-world examples. By the end of this journey, you will have a profound understanding of how CAPA can be a game-changer for your organization's quality management.
The Essence of CAPA
At its core, CAPA is a systematic approach to addressing issues, anomalies, or non-conformities in processes, products, or services within an organization. It is an indispensable component of Quality Management Systems (QMS) that ensures continuous improvement, regulatory compliance, and customer satisfaction.
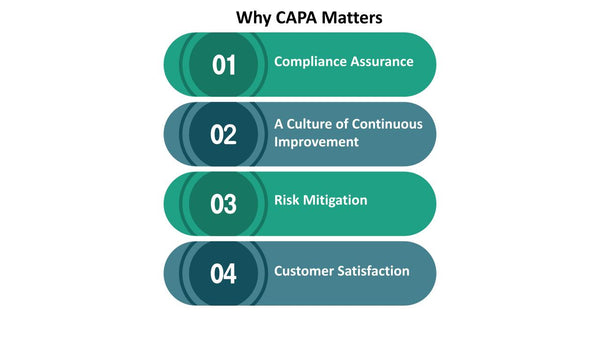
Why CAPA Matters
The importance of CAPA cannot be overstated, and here's why:
-
Compliance Assurance
In various industries, regulatory compliance is not a choice but a necessity. CAPA plays a pivotal role in ensuring organizations adhere to specific standards and regulations. It acts as a safety net, helping organizations rectify deviations promptly.
-
A Culture of Continuous Improvement
CAPA is not just about fixing issues; it's about fostering a culture of continuous improvement. By systematically identifying problems, analyzing their root causes, and implementing corrective and preventive actions, organizations can optimize their processes, enhance product quality, and bolster customer satisfaction.
-
Risk Mitigation
In a world where risks lurk around every corner, CAPA is a shield against unforeseen troubles. Timely corrective actions can prevent minor issues from escalating into major problems, saving organizations from costly setbacks.
-
Customer Satisfaction
Customers are the lifeblood of any business. Effective CAPA processes lead to higher product and service quality, translating to increased customer satisfaction. Satisfied customers are more likely to stay loyal and advocate for your brand.
Key Steps in CAPA Implementation
Implementing CAPA effectively involves a series of well-defined steps:
-
Issue Identification
The journey begins with the identification of issues, anomalies, or non-conformities. These issues can surface through customer complaints, internal audits, quality inspections, or the analysis of performance data.
-
Root Cause Analysis (RCA)
Identifying the root cause of a problem is fundamental. Root Cause Analysis (RCA) techniques, such as the "5 Whys" method or Ishikawa diagrams, are employed to delve deep into the factors contributing to the issue.
-
Corrective Action
Corrective Action is all about addressing the immediate issue head-on. It involves devising and implementing swift solutions to rectify the problem and prevent its recurrence. This may necessitate process changes, product recalls, or retraining of personnel.
-
Preventive Action
Beyond addressing the current issue, organizations must take proactive measures to prevent similar issues from arising in the future. Preventive Action involves systemic improvements to processes, training, or documentation.
-
Verification
Verification ensures the efficacy of the corrective and preventive actions taken. It involves assessing whether these actions have successfully addressed the issue and prevented its recurrence. Verification may include testing, data analysis, or continuous process monitoring.
-
Documentation
Robust documentation is the backbone of the CAPA process. Comprehensive records of issue identification, root cause analysis, corrective and preventive actions, verification results, and any subsequent follow-up activities must be maintained.
-
Monitoring and Review
CAPA is not a one-time event but an ongoing process. Regular monitoring and review of the implemented actions are crucial to ensure sustained effectiveness. Adjustments may be necessary based on performance data and feedback.
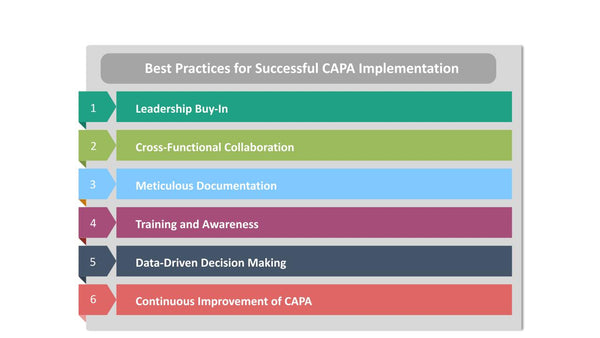
Best Practices for Successful CAPA Implementation
To ensure the success of your CAPA process, consider these best practices:
-
Leadership Buy-In
Strong support and commitment from top management are essential for the effective implementation of CAPA. Leaders should set the tone for a culture of quality and continuous improvement.
-
Cross-Functional Collaboration
Involve cross-functional teams in the CAPA process. This diversity of perspectives and expertise ensures a comprehensive understanding of the issue and leads to more effective solutions.
-
Meticulous Documentation
Organized and thorough documentation is non-negotiable. It provides a clear trail of the entire CAPA process, including detailed records of all actions taken, timelines, and responsible individuals or teams.
-
Training and Awareness
Ensure that employees are well-trained in CAPA procedures and understand their roles in the process. Creating awareness about the importance of CAPA in achieving quality and compliance goals is equally crucial.
-
Data-Driven Decision Making
Leverage data and metrics throughout the CAPA process. Data provides objective insights into the effectiveness of actions taken and helps in making informed decisions.
-
Continuous Improvement of CAPA
Apply the principles of continuous improvement to your CAPA process itself. Regularly review and enhance your CAPA procedures based on feedback and performance data
Real-World Examples of CAPA
To gain a more concrete understanding of how CAPA operates in real-world scenarios, let's explore two practical examples:
-
Pharmaceutical Industry
In the pharmaceutical industry, where human lives are at stake, CAPA is a lifeline. Imagine a situation where a batch of medication is found to have a quality issue, such as contamination or incorrect dosage. A CAPA process swings into action. It begins with pinpointing the root cause of the problem, followed by the immediate recall of affected products. Corrective actions involve scrutinizing the manufacturing process, implementing necessary changes, and reevaluating quality control procedures. Preventive actions focus on ensuring that such issues never occur again, often leading to enhanced quality assurance protocols and more rigorous testing.
-
Manufacturing Industry
In the manufacturing sector, CAPA is indispensable for maintaining product quality and customer satisfaction. Let's consider a company that produces electronic components. They observe a disturbingly high rate of defects in a specific product line. Initiating CAPA, the company delves deep into the issue. Root cause analysis reveals that a crucial machine on the production line is malfunctioning. Corrective action swiftly follows with the repair or replacement of the malfunctioning machine. Preventive actions, in this case, include instituting a regular maintenance schedule and training operators to identify and report machine issues promptly. These measures significantly reduce the likelihood of future defects.
Challenges in Implementing CAPA
While CAPA offers a powerful framework for improving quality, it comes with its share of challenges:
-
Resistance to Change
Introducing CAPA often requires changes in processes, workflows, and sometimes even the corporate culture. Resistance to these changes can hinder the smooth adoption of CAPA.
-
Resource Constraints
Effective CAPA implementation demands time, personnel, and financial resources. Organizations with limited resources may struggle to allocate them adequately to the CAPA process.
-
Complex Root Cause Analysis
Uncovering the true root cause of an issue can be challenging. It may involve intricate investigations and the integration of data from various sources.
-
Overreliance on Documentation
While documentation is vital, overemphasis on paperwork can lead to a bureaucratic CAPA process, making it less agile and efficient.
-
Inadequate Training
If employees are not adequately trained in CAPA procedures, the process may not yield the desired results. Effective training is crucial.
Conclusion
Corrective and Preventive Action (CAPA) stands as a cornerstone of quality management, ensuring compliance, continuous improvement, risk mitigation, and customer satisfaction. Successful CAPA implementation requires leadership support, cross-functional collaboration, meticulous documentation, employee training, data-driven decision-making, and a commitment to continuous improvement. Real-world examples illustrate CAPA's transformative impact across industries. It is not merely a tool for crisis management but a strategic approach to sustainable quality enhancement. In an era where quality defines competitiveness, CAPA empowers organizations to thrive by adapting and evolving. Regardless of the industry, CAPA is the key to a future defined by quality-driven success.