CGMP Certification: Ensuring Quality and Safety in Pharmaceuticals
In the pharmaceutical industry, where the health and well-being of patients are paramount, ensuring the quality and safety of drugs is a top priority. Current Good Manufacturing Practice (CGMP) certification plays a pivotal role in achieving this goal. In this blog post, we will explore CGMP certification, its significance in pharmaceutical manufacturing, the key principles it encompasses, and its impact on the industry's ability to deliver safe and effective medications.
Understanding CGMP: A Pillar of Pharmaceutical Quality
CGMP, which stands for Current Good Manufacturing Practice, is a set of regulations and guidelines established by regulatory authorities to ensure the consistent quality and safety of pharmaceutical products. CGMP regulations are not confined to a single country; they are recognized and adhered to globally, making them a cornerstone of pharmaceutical manufacturing standards.
The primary objective of CGMP is to prevent the production of unsafe or substandard pharmaceutical products, including prescription medications, over-the-counter drugs, biologics, and dietary supplements. These regulations provide a framework for pharmaceutical manufacturers to maintain high-quality standards throughout the production process, from the sourcing of raw materials to the distribution of finished products.
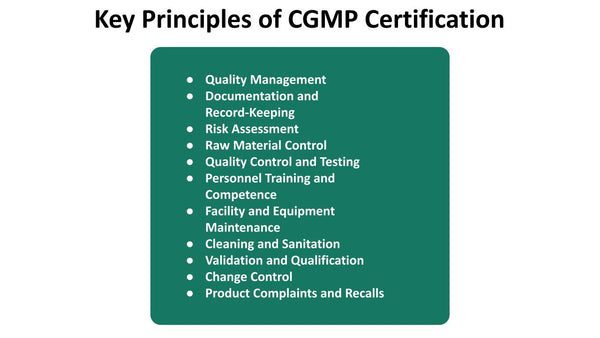
Key Principles of CGMP Certification
To achieve and maintain CGMP certification, pharmaceutical manufacturers must adhere to a set of core principles and practices. These principles are designed to ensure consistency, reliability, and compliance with regulatory requirements:
- Quality Management: CGMP emphasizes the importance of a robust quality management system (QMS) that encompasses all aspects of manufacturing, including planning, production, testing, and distribution. This system should be designed to identify, mitigate, and prevent quality issues.
- Documentation and Record-Keeping: Manufacturers are required to maintain detailed documentation and records of all aspects of the manufacturing process, from production methods to quality control measures. Accurate record-keeping is essential for traceability and accountability.
- Risk Assessment: CGMP encourages manufacturers to assess and manage risks associated with pharmaceutical production. This includes evaluating potential hazards and implementing strategies to mitigate them.
- Raw Material Control: Manufacturers must establish procedures for the sourcing and control of raw materials. This includes verification of the quality and integrity of materials used in drug production.
- Quality Control and Testing: Rigorous quality control measures are essential to ensure the identity, strength, quality, and purity of pharmaceutical products. CGMP mandates regular testing of raw materials, in-process samples, and finished products.
- Personnel Training and Competence: Manufacturers are responsible for ensuring that their personnel are adequately trained and competent to perform their roles in compliance with CGMP requirements.
- Facility and Equipment Maintenance: CGMP mandates the maintenance and calibration of manufacturing facilities and equipment to ensure that they meet defined quality standards.
- Cleaning and Sanitation: Proper cleaning and sanitation practices are crucial to prevent cross-contamination and ensure the integrity of pharmaceutical products.
- Validation and Qualification: Manufacturers must validate and qualify critical manufacturing processes, equipment, and systems to ensure their reliability and consistency.
- Change Control: Any changes in manufacturing processes, equipment, or materials must be carefully evaluated, documented, and approved to prevent potential quality issues.
- Product Complaints and Recalls: Manufacturers must have procedures in place to investigate and address product complaints and recalls promptly.
Significance of CGMP Certification
CGMP certification is of utmost significance in the pharmaceutical industry for several compelling reasons:
- Patient Safety: CGMP certification ensures that pharmaceutical products are safe, effective, and free from contaminants. It safeguards the health and well-being of patients who rely on these medications.
- Regulatory Compliance: Regulatory authorities, such as the U.S. Food and Drug Administration (FDA) and the European Medicines Agency (EMA), require pharmaceutical manufacturers to comply with CGMP regulations. Non-compliance can result in regulatory sanctions, product recalls, and damage to a manufacturer's reputation.
- International Recognition: CGMP regulations are recognized worldwide, making CGMP-certified pharmaceutical products eligible for export to global markets.
- Product Quality: CGMP certification promotes the production of high-quality pharmaceuticals, fostering consumer confidence and trust in the industry.
- Innovation and Research: By ensuring consistent product quality and safety, CGMP certification encourages research and development in the pharmaceutical sector, driving innovation and the discovery of new treatments and therapies.
The CGMP Certification Process
The process of obtaining CGMP certification is comprehensive and involves several key steps:
- Preparation: Pharmaceutical manufacturers begin by evaluating their current manufacturing processes, quality systems, and documentation procedures to identify areas of improvement. This stage often involves a gap analysis to determine the extent of compliance with CGMP requirements.
- Training and Education: Employees at all levels receive training on CGMP regulations and principles to ensure a common understanding of compliance requirements.
- Quality Management System (QMS) Implementation: Manufacturers establish or enhance their QMS to align with CGMP principles. This includes the development of standard operating procedures (SOPs), documentation practices, and quality control measures.
- Audit and Self-Assessment: Manufacturers conduct internal audits and self-assessments to identify and rectify non-compliance issues. This stage aims to ensure that the organization is prepared for external audits.
- Selection of Certification Body: Manufacturers choose a recognized certification body or authority to conduct an external audit and assess compliance with CGMP standards.
- External Audit: A team of auditors from the certification body conducts an on-site audit of the manufacturer's facilities, processes, and documentation. The audit assesses compliance with CGMP regulations and identifies any non-conformities.
- Corrective Actions: Manufacturers address any non-conformities identified during the audit and implement corrective actions to rectify deficiencies in their quality systems or processes.
- Certification: If the external audit results demonstrate compliance with CGMP requirements, the certification body issues CGMP certification to the manufacturer.
- Ongoing Compliance: Maintaining CGMP certification requires ongoing adherence to regulatory standards, including periodic surveillance audits and updates to the quality management system as needed.
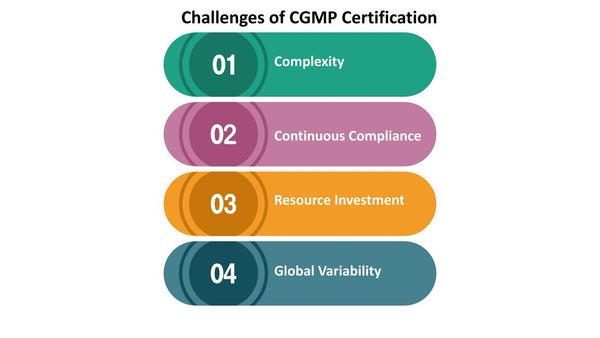
Challenges of CGMP Certification
While CGMP certification is essential for pharmaceutical manufacturers, it comes with several challenges:
- Complexity: Achieving and maintaining CGMP certification involves navigating a complex and highly regulated environment, requiring significant expertise and resources.
- Continuous Compliance: Maintaining CGMP certification requires an ongoing commitment to compliance and the ability to adapt to evolving regulatory requirements.
- Resource Investment: The implementation of CGMP-compliant quality management systems and processes often requires substantial financial and personnel resources.
- Global Variability: Different countries may have specific interpretations or variations of CGMP regulations, necessitating compliance with multiple sets of standards for international markets.
Conclusion
In the pharmaceutical industry, CGMP certification serves as a cornerstone for ensuring the quality, safety, and effectiveness of medications. By adhering to CGMP principles, pharmaceutical manufacturers can produce high-quality products that meet regulatory requirements, protect patient health, and maintain the trust of healthcare professionals and consumers. While the certification process presents challenges, its benefits are immeasurable, contributing to the advancement of healthcare and pharmaceutical innovation worldwide. CGMP certification is not just a regulatory requirement; it is a commitment to excellence and patient well-being.