CAPA Explained: The Acronym and Its Quality Benefits
In the dynamic world of quality management and regulatory compliance, CAPA stands as a critical acronym that holds immense significance for organizations across various industries. CAPA stands for Corrective and Preventive Actions, a structured and systematic approach to identifying, addressing, and preventing issues that can affect product quality, compliance, and overall business performance. In this comprehensive guide, we will explore the world of CAPA, exploring its meaning, importance, key components, best practices, and how organizations can leverage it to enhance quality, compliance, and continual improvement.
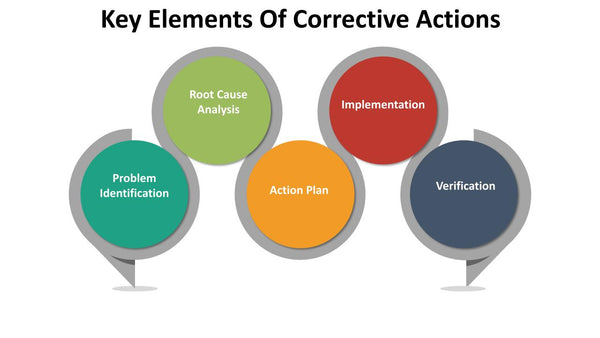
Chapter 1: Understanding CAPA
CAPA, or Corrective and Preventive Actions, is a fundamental concept in quality management systems (QMS) and regulatory compliance. It represents a structured methodology for addressing problems, non-conformities, and deviations from established standards or procedures. The main objectives of CAPA are:
- Correcting issues to prevent their recurrence.
- Preventing potential issues from happening in the first place.
- Continuously improving processes and products.
CAPA is not merely a reactive process; it's a proactive approach to quality management that encompasses both corrective and preventive measures.
Chapter 2: Corrective Actions
Corrective actions are a crucial aspect of CAPA. They are designed to address issues that have already occurred and have been identified through various means, such as customer complaints, internal audits, inspections, or incident reports.
Key elements of corrective actions include:
- Problem Identification: Identifying the issue, its root cause, and the impact on quality and compliance.
- Root Cause Analysis: Delving deep into the problem to identify the underlying factors that caused it. Common tools for root cause analysis include the "5 Whys" and Fishbone Diagrams.
- Action Plan: Develop a comprehensive action plan to address the issue effectively. The plan outlines the specific steps to be taken, responsibilities, timelines, and resources required.
- Implementation: Executing the action plan to resolve the immediate issue. This may involve process changes, training, or product recalls.
- Verification: Confirm that the corrective actions have been successful in eliminating the problem. This may involve retesting, inspections, or data analysis.
Chapter 3: Preventive Actions
While corrective actions focus on addressing existing problems, preventive actions aim to identify and eliminate the root causes of potential issues before they occur.
Key elements of preventive actions include:
- Risk Assessment: Identifying potential risks and vulnerabilities within processes, products, or systems that could lead to future issues.
- Proactive Measures: Developing and implementing proactive measures to prevent identified risks from materializing. This may include process improvements, enhanced training, or product design changes.
- Monitoring and Auditing: Regularly monitoring and auditing processes to ensure that preventive measures are effectively reducing the risk of issues.
- Continuous Improvement: Promoting a culture of continuous improvement by reviewing the effectiveness of preventive actions and making necessary adjustments.
Chapter 4: CAPA in Regulatory Compliance
CAPA plays a vital role in ensuring regulatory compliance, especially in highly regulated industries such as healthcare, pharmaceuticals, and aerospace. Regulatory bodies like the FDA (Food and Drug Administration) require organizations to have robust CAPA processes in place to:
- Address deviations from regulatory requirements.
- Investigate product quality issues.
- Implement corrective actions to prevent recurrence.
- Demonstrate compliance with regulations through documentation.
Chapter 5: Benefits of Implementing CAPA
Implementing a robust CAPA system offers numerous benefits to organizations:
- Improved Quality: CAPA helps organizations identify and address quality issues, leading to improved product quality and customer satisfaction.
- Reduced Costs: By preventing problems and defects, CAPA reduces the cost of rework, recalls, and customer complaints.
- Compliance: CAPA ensures that organizations meet regulatory requirements and maintain compliance with industry standards.
- Enhanced Reputation: Effective CAPA processes demonstrate a commitment to quality and customer satisfaction, enhancing an organization's reputation.
- Risk Management: CAPA helps organizations identify and mitigate risks, reducing the likelihood of costly incidents or regulatory violations.
- Data-Driven Decision-Making: CAPA processes provide valuable data and insights that can inform strategic decision-making and continuous improvement initiatives.
Chapter 6: Best Practices in CAPA Implementation
Successful CAPA implementation relies on the following best practices, including:
- Management Commitment: Ensuring top management's commitment to CAPA is vital for allocating resources and fostering a culture of quality.
- Training and Education: Providing training and education to employees involved in CAPA processes to enhance their skills in problem-solving and root cause analysis.
- Documentation: Maintaining detailed records of all CAPA activities, including problem reports, investigations, action plans, implementation details, and verification results.
- Cross-Functional Teams: Involving cross-functional teams in CAPA activities to gain diverse perspectives and expertise.
- Technology Utilization: Leveraging technology and CAPA software to streamline processes, track progress, and enhance data analysis.
Chapter 7: Challenges and Considerations
While CAPA offers significant benefits, it is not without its challenges and considerations:
- Resource Allocation: Implementing and maintaining CAPA processes can require significant time, manpower, and financial resources.
- Complexity: CAPA processes can be complex, and organizations may need specialized expertise to navigate them effectively.
- Cultural Change: Achieving a culture of quality and continuous improvement may require a shift in organizational culture and mindset.
- Documentation Burden: Maintaining comprehensive documentation throughout the CAPA process can be time-consuming.
Chapter 8: Continuous Improvement and CAPA
CAPA itself is a continuous improvement CAPA process. Organizations should regularly review and enhance their CAPA processes to adapt to evolving needs and challenges. This includes:
- Performance Metrics: Defining key performance indicators (KPIs) to measure the effectiveness of CAPA processes, such as the time to resolution, recurrence rates, and cost savings.
- Root Cause Analysis of CAPA: Continuously analyzing the CAPA process itself to identify opportunities for improvement and efficiency gains.
- Employee Feedback: Seeking feedback from employees involved in CAPA processes to identify pain points and areas for enhancement.
Conclusion
Corrective and Preventive Actions (CAPA) represent a cornerstone of effective quality management and regulatory compliance in organizations. By understanding the principles and best practices of CAPA implementation, organizations can address existing issues, prevent future problems, enhance product quality, reduce costs, and maintain compliance with regulatory requirements. CAPA is not merely a process; it's a commitment to a culture of quality, continuous improvement, and excellence that can drive an organization's success and customer satisfaction.