ISO 45001 Improvement Plan Template
Introduction
Improvement plans are essential for any organization seeking to maintain compliance with ISO 45001 standards. A well-thought-out improvement plan can help businesses identify areas for growth, set clear objectives, and track progress over time. This template provides a structured framework for developing an effective improvement plan that aligns with the requirements of ISO 45001. This template allows Organizations to streamline their improvement efforts and enhance their occupational health and safety management systems.
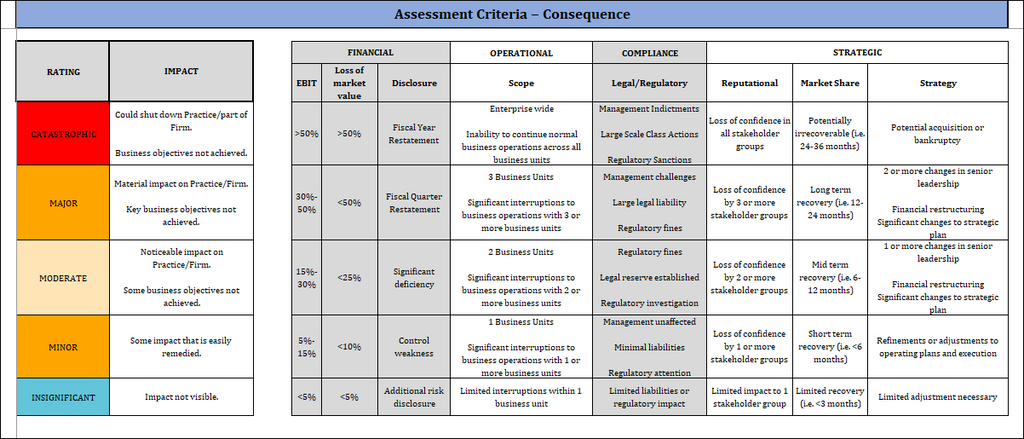
Purpose Of Improvement Plan
An improvement plan is essential for setting clear goals and objectives for individuals or teams within an organization to enhance performance and productivity. By outlining specific areas that need improvement and the actions required to achieve desired results, the improvement plan provides a roadmap for continuous growth and development. It helps to identify strengths and weaknesses and to create strategies for bridging gaps and overcoming challenges.
Additionally, an improvement plan promotes accountability and transparency by clearly outlining responsibilities and timelines, enabling monitoring and evaluating progress toward goals. Ultimately, an improvement plan aims to drive positive change, foster a culture of continuous improvement, and maximize the potential of individuals and teams within an organization.
Objectives Of Improvement Plan For ISO 45001 Template
1. To identify and assess risks and hazards in the workplace to prevent workplace injuries and illnesses.
2. To develop and implement adequate controls and measures to mitigate risks and hazards.
3. To enhance employee involvement and consultation in health and safety matters.
4. To establish clear roles and responsibilities for health and safety management within the organization.
5. To ensure compliance with legal and regulatory occupational health and safety requirements.
6. To continuously monitor and evaluate the effectiveness of the occupational health and safety management system.
7. To communicate and raise awareness of health and safety policies and procedures among employees.
8. To provide adequate employee training and resources to implement health and safety measures effectively.
9. To establish mechanisms for reporting and investigating incidents and near misses.
10. To establish a culture of continuous improvement in occupational health and safety practices.
Implementing And Monitoring The Improvement Plan
Implementing and monitoring the improvement plan involves several key steps:
1. Communicate The Improvement Plan To All Stakeholders: Ensure all team members know the goals, objectives, and timeline. This will help in fostering buy-in and commitment from everyone involved.
2. Assign Responsibilities And Set Deadlines: Clearly define each team member's roles and responsibilities in implementing the improvement plan. Set realistic deadlines for each task to ensure timely progress.
3. Provide Necessary Resources And Support: Ensure team members access the resources, training, and support needed to implement the improvement plan successfully. This may include additional training, tools, or software.
4. Monitor Progress Regularly: Establish a system for tracking the progress of the improvement plan. This could involve regular check-ins, progress reports, or milestone meetings to ensure the plan is on track.
5. Address Any Issues Or Roadblocks: Be proactive in addressing any challenges or obstacles that may arise during the implementation of the improvement plan. Encourage open communication and collaboration to find solutions and keep the plan moving forward.
6. Evaluate And Adjust As Needed: Periodically evaluate the effectiveness of the improvement plan and make adjustments as necessary. This may involve revising goals, timelines, or strategies based on feedback and results.
Following these steps, you can effectively implement and monitor the improvement plan to achieve the desired outcomes and drive continuous organizational improvement.
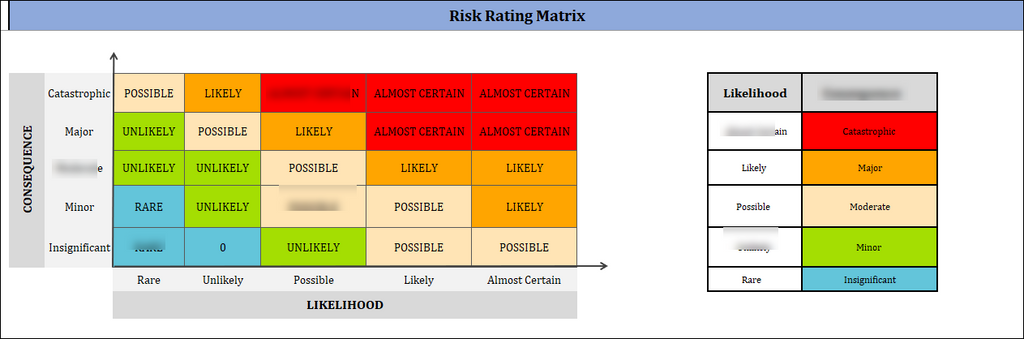
Best Practices For Using Improvement Plan
1. Clearly Define Goals And Objectives: Before creating an improvement plan, clearly outline what specific areas need improvement and set measurable goals and objectives.
2. Involve The Learner: Engage the individual in creating the improvement plan to ensure they are invested in their development and success.
3. Identify Strengths And Weaknesses: Conduct a thorough assessment to identify the learner's strengths and areas for improvement. This will help tailor the improvement plan to the learner's specific needs.
4. Provide Resources And Support: Offer the learner the necessary resources, tools, and support to help them achieve their improvement goals. This could include additional learning materials, tutoring time, or language-learning software access.
5. Monitor Progress And Provide Feedback: Regularly track the learner's progress towards their improvement goals, provide constructive feedback, and adjust the plan as needed.
6. Encourage Reflection And Self-assessment: Encourage the learner to reflect on their progress, identify areas for further improvement, and take ownership of their learning journey.
7. Celebrate Achievements: To motivate and encourage continued progress, recognize and celebrate the learner's successes and milestones throughout the improvement plan.
8. Continuously Assess And Adjust The Plan: Review the effectiveness of the improvement plan regularly and make any necessary adjustments to ensure it remains relevant and practical.
Conclusion
In conclusion, implementing an improvement plan for ISO 45001 is crucial for maintaining a safe and compliant work environment. This template provides a structured approach to enhancing your occupational health and safety management system. By following this plan and making necessary adjustments, your organization can ensure continuous improvement and adherence to ISO 45001 standards. Download the improvement plan template to streamline your processes and achieve safety excellence.